产品列表
联系我们
- 苏州率尔捷机电科技有限公司
- 电话:0512-65969213
- 传真:0512-65969213
- 手机:18936081853
- 地址:苏州工业园区葑亭大道668号
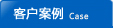
您当前位置:网站首页 -> 客户案例
提高数控电火花机床加工效率的措施
作者: 日期:2012/10/30 19:37:02 人气:3205
提高数控电火花机床加工效率的措施
数控电火花机床加工效率直接相关的三大方面:电火花加工工艺、数控电火花加工机床的调整、电火花加工操作。根据这三方面详细探讨了提高电火花加工效率的工艺措施,希望可帮助企业解决一些实际问题。
1数控电火花加工工艺相关的要点
1.1要用机械加工去除大部分材料
工件的加工部位在进行电火花加工之前,要先用机械加工方法进行粗加工,仅将刀具精铣困难或无法精铣的部位留给电火花加工,这样能使电火花加工的材料量大为减少,可大幅度提高电火花加工效率。
如怕工作的麻烦,不进行机械粗加工就直接进行电火花加工,会导致电火花加工的效率极其低下,这就需正确认识电火花加工这种工艺方法的加工速度。电火花加工是靠微观的热融化过程一点点蚀除材料的,比起机械切削加工去除材料的过程要慢得多。对于大的型腔,即使是进行了机械粗加工,如给电火花加工留的余量过多也会降低加工效率。
2根据加工情况决定工艺方法
电火花加工有单电极直接成形工艺、多电极更换成形工艺等。选择工艺时不仅要考虑加工速度,还应详细考虑加工精度和表面粗糙度要求。单电极直接成形工艺只用一只电极加工出所需的型腔形状,这种工艺方法用于加工形状简单、精度要求不高的型腔,不需进行重复的装夹操作,可提高电火花加工的效率。对于加工要求较高的场合,通常采用多电极加工的工艺方法。首先用粗加工电极蚀除大量材料,然后用精加工电极进行精加工,精加工时还可考虑换用多个电极来补偿电极的损耗。
如在精度要求较高的加工场合,只使用一只电极来进行加工,这种因对工艺认识不够,本想通过减少电极数目来提高加工效率,而实际在加工过程却因为不能选用较大的电参数进行粗加工,导致加工的效率极其低下;另一种情况是,在加工要求不高的情况下,使用多个电极来进行加工,也必然会降低加工效率。
1.3合理选用电极材料
电极材料的选取直接关系到放电的效果,在很大程度上,材料的选取是否恰当,决定了放电速度、加工精度及表面粗糙度的最终情况。应根据不同类型模具加工的实际需求,有针对性地进行电极材料的选用。电火花加工通常使用紫铜电极和石墨电极。很多模具企业在选择电极材料时,很少进行考虑,大小电极一律习惯选用同种电极材料,这种做法会影响电火花加工的效率。
紫铜做电极较容易获得稳定的加工状态,可获得轮廓清晰的型腔,加工表面粗糙度值低,通常适用于低损耗的加工条件,由于低损耗加工的平均电流较小,且不适合大电流加工,其生产率并不高;石墨电极在加工蚀除量较大的情况下能实现低损耗、高速粗加工,但在精加工中放电稳定性较差,容易过渡到电弧放电,因而能选取损耗较大的加工参数来加工。
大多企业使用紫铜作为电极材料。而根据加工经验,使用石墨电极加工锻模的大型腔,其加工速度高,比使用紫铜电极可节省约1/3的时间;也有些企业认识到石墨电极的优越性,不分场合习惯选用石墨电极,导致模具在表面粗糙度要求低于的加工场合,始终难以稳定地达到加工要求,于是反复进行返修加工,极大地降低了加工效率,如选用紫铜电极,问题将会迎刃而解。可见选择电极材料时,应根据加工要求作出合理的选择。
1.4确定适当的电极缩放量
电极缩放量的选取要考虑多方面的因素。电火花加工有平动和不平动两种加工方式,数控电火花加工机床一般都可进行平动加工,而传统电火花加工机床如没有安装平动头就不能进行平动加工。这两种加工方式的电极缩放量选取是有区别的。
在不采用平动加工时,加工尺寸主要取决于精加工的控制。确定精加工电极缩放量时应先考虑好为达到预定表面粗糙度要选用的电参数条件,明确该条件下火花间隙的大小,再确定电极缩放量,一般取单侧0.02~0.06mm;确定粗加工电极缩放量时以考虑加工速度和为精加工预留适当余量为标准,一般取单侧0.15~0.25mm。
在采用电极平动加工时,加工的尺寸精度取决于对放电间隙、电极缩放量和平动量的控制。由于平动量的大小是可控的,所以可根据放电间隙的大小调节平动量,这样较容易控制加工的尺寸,电极缩放量的大小也就可相对大一些,尤其是在精加工时;总之可根据具体情况来灵活选取。粗加工中一般不用平动加工,电极缩放量取单侧0.15~0.30mm。精加工采用多段加工条件用平动的方法来改善排屑状况,达到稳定的加工,可获得侧面与底面更均匀的表面粗糙度。电极的缩放量常取0.05~0.15mm。
模具的电火花加工中,通常会因电极缩放量取得太小不能选用较大的放电条件而导致加工效率低下。如在加工允许的情况下,粗加工电极的缩放量取单侧0.30mm选用的电参数比取单侧0.15mm的电参数要提高速度在2~3倍以上。平动加工时精加工电极可根据加工情况,适当增大电极缩放量有利于提高加工速度。必须注意,增大电极缩放量后必须相应提高放电参数的能量,且不可盲目增大电极缩放量,否则反而会降低加工效率。如粗加工将电极缩放量取单侧0.80mm,而实际加工虽选择了较大的放电参数,但实际的放电间隙可能只有单侧0.30mm左右,那么将会为后续加工留下了较多的材料余量,必将降低加工效率。数控电火花加工机床如按传统机床的电极缩放方法,不利用平动加工的功能,必将降低加工效率,尤其是在精加工中。如电极缩放量取单侧0.03mm,那么只能选用一个较小的放电参数进行加工,如粗加工中的材料余量稍多的话,甚至可能产生无法加工的情况;如将电极缩放量增加到单侧0.08mm,那么加工的放电参数可增大,可很快地将材料余量去除,然后再利用平动功能来逐步修光侧面。对于加工电极是圆形、方形的更应如此。普通加工中适当增大电极缩放量并不会对形状造成多大影响,精密加工时才应特殊对待。
1.5电极设计考虑"面积效应"
"面积效应"是指电火花加工中因加工面积变化引起加工速度等工艺指标变化的效应。当电火花加工的面积小到某一临界值时,加工速度会显著降低。因为加工面积小,在单位面积上脉冲放电过分集中,致使放电间隙的电蚀产物排除不畅,同时,会产生气体排除液体的现象,造成放电加工在气体介质中进行,而大大降低加工速度。因此设计电极时要考虑不要拆分加工面积太小的电极,多使用整体式电极。但也要注意,当整体式电极面积较大,且加工深度较深、排屑困难的情况下,应考虑将整体电极分拆成几个电极进行分次加工,可根据型腔的几何形状把电极分解成主型腔电极和副型腔电极。否则在加工中会出现放电不稳定的情况,导致加工效率低下、精度难以保证等不良情况。
2数控电火花加工机床调整的要点
2.1电参数的调节
电参数选择的好坏,直接影响加工的各项工艺指标。电参数调节的最终目的是为了达到预定的加工尺寸、表面粗糙度要求,达到较高的加工效率。电参数调节时应考虑:电极数目、电极损耗、加工表面粗糙度要求、电极缩放量、加工面积、加工深度等基本因素。
目前数控电火花加工机床的智能性已有了很大的提高,机床储存有针对各种材料组合加工的大量成套参数,只需在编程过程中按编程要求输入工艺条件,即可自动选择、配置电参数。加工中机床依靠智能化控制技术(如"模糊控制"技术),由计算机监测、判断加工间隙的状态,自动微调电参数,保持稳定的放电加工,达到较高的加工效率。先进的智能化电火花加工机床的电参数数据库能满足一般加工要求,且极大地降低了机床对操作人员的技能要求。而传统电火花加工机床要求操作者具有丰富的工作经验,能根据加工要求灵活配置电参数。
机床的智能控制技术并不是万能的,故不能忽视人工调整电参数的作用。尤其像在深孔加工、大锥度加工、大面积加工等一些较特殊的加工场合,人工调整电参数就显得很有必要。调整电参数时,应优先考虑调整电参数主规准以外的参数,如抬刀高度、放电时间、抬刀速度等;其次可按次序考虑调整脉冲间隔、脉冲宽度、加工电流等,特殊材料加工可试用负极性加工(电极为负极)。在加工状态稳定的前提下,减少抬刀动作及幅度、降低脉冲间隔、增大加工电流有利于提高加工效率。但在加工不稳定的情况下,一定要保持勤抬刀,适当选用较大的脉冲间隔,否则反而会降低加工效率,甚至引起电弧放电,使加工过程不能正常进行。根据加工经验,适当保守地进行电参数的调节,可维持加工的正常进行,且可获得较高的加工效率。
脉冲宽度对加工速度有较大的影响,但一些技术人员在认识脉冲宽度对加工速度的影响上存在误区。有的认为将脉冲宽度增大可提高加工速度,有的则认为将脉冲宽度降低可提高加工速度。理论上:脉冲峰值电流一定时,脉冲宽度增加,加工速度随之增加,脉冲宽度增加到一定数值时,加工速度最高,此后再继续增加脉冲宽度,加工速度反而下降。但在实际生产中,对脉冲宽度必须要有一个量的认识。根据大量的加工实例,这里必须指出:最高加工速度对应的脉冲宽度往往很小,因此电极损耗较大,在很多情况下不宜采用,而实际加工中机床选配的电规准一般都考虑到降低电极损耗。那么,在低损耗加工规准中,如加大脉冲宽度,加工速度必然降低,降低脉冲宽度,加工速度会得到一定程度的提升。
2.2加工留量的控制
数控电火花加工是用多个条件段来进行加工的,条件段之间要有一定的加工留量。如加工要求的深度为5mm,电极缩放量为单侧0.15mm。设使用的电规准从大到小分3段来进行加工,则根据各档电规准放电间隙的大小来设置进给深度和平动半径:第一个规准进给深度为4.85mm,平动半径为0.02mm,第二个规准进给深度为4.92mm,平动半径为0.13mm,第三个规准进给深度为4.97mm,平动半径为0.17mm。各条件段之间加工留量大小的控制与加工效率有很大的关系。适当减少加工留量能提高电火花加工效率,尤其是在大面积的精加工场合作用显著。如将上例中第一个规准进给深度改为4.90mm,平动半径为0.10mm,第二个规准进给深度为4.95mm,平动半径为0.15mm,第三个规准不变,则可在一定程度上提高加工效率。
数控电火花加工机床自动编程时给出的加工留量,是以保证表面粗糙度为前提的,相对来说较保守,为了进一步提高加工效率,可根据加工要求修改自动编程生成程序的加工留量。但必须注意,减少加工留量必须要保证下一个加工规准能修光上一个加工规准。另外,减少加工留量对小面积加工的效率提高意义并不大。
2.3平动加工的选择
平动加工是数控电火花加工的一种重要工艺方法。不同的数控电火花加工机床其平动加工的方式有所区别,应根据所用机床灵活、合理应用平动加工。某数控电火花加工机床的平动加工方式有两种:自由平动和伺服平动。自由平动是指主轴伺服加工时,另外两轴同时按一定轨迹作扩大运动,一直加工到指定深度。伺服平动是指主轴加工到指定深度后另外两轴按一定的轨迹作扩大运动。自由平动一般用于浅表加工,加工时边打边平动可改善排屑性能,提高加工速度,减少积碳;但对于深度较深的场合,却会降低加工速度,增大电极的边角损耗。伺服平动一般用于加工深度较深的加工场合,先加工完底面再修侧面,深度较浅时其加工效果不如自由平动,它也常用在加工型腔侧壁的沟槽、环,还可用在其他两轴平动的场合等。
2.4定时加工
数控电火花加工机床一般都具有定时加工功能,可用于控制面积较大电极精加工的最后几段电参数的加工时间。精加工时电火花的电蚀能力非常弱,由于间隙内加工屑及其他因素的影响,需很长的加工时间。由于最后几个条件的尺寸变化已很小,实际上我们只要加工到要求的表面粗糙度后就可结束加工,可根据经验采用定时加工方法,这样可大幅度地提高精加工效率。
2.5改变垂直伺服加工的方法
目前大多数控电火化加工机床可实现横向加工、多轴联动加工。但这些功能在模具企业中并没有得到很好的应用。如能充分发挥机床的功能,可使机床的加工效率得到提高。如注塑模的成形镶件四周有较薄、较深的胶位,这些部位如采用Z轴伺服加工,会因局部放电面积小,加工深度大,加工过程中就会发生放电不稳定的现象,加工速度缓慢。若通过改善工艺方法,利用数控电火花加工机床的横向伺服功能,使电极作横向伺服加工,加工速度可比采用Z轴伺服加工提高数倍。模具"清角加工"因加工部位面积小而发生放电不稳定的现象,采用X、Y、Z3轴联动的方法,即斜向加工,可使放电加工稳定,提高加工效率。
3数控电火花加工操作的要点
3.1提高重复定位精度
模具电火花加工往往需使用很多个电极进行,这时需进行重复定位。实际加工中,重复定位精度也是影响加工效率的一个重要因素,这些情况主要发生在精加工中。如第一个电极在对深度时没有对准,导致第一次加工的深度浅了,那么第二次加工在必须保证加工深度的情况下,要加工的材料量必然增加,精加工中又不能选用大的电规准,这就导致了加工效率低下。根据加工经验,如像接近30cm2的大面积加工,在精加工规准下,多加工0.02mm的深度,将花费1h以上的加工时间;还有如第一个电极加工完成后,第二个电极加工的位置与第一个电极的加工位置存在较大差别,一个侧面修不到,另一个侧面的加工量增多,这种情况也会降低加工效率。
利用电极与工件进行接触感知的定位方法在模具企业被广泛采用。这种定位方法相对简单,是操作人员非常熟悉的。但这种定位方法的误差较大,难以保证稳定的定位精度,因定位超差导致的加工异常问题时有发生,降低了加工效率。为了提高重复定位精度,可采用间接定位方法。如利用基准球进行间接定位,这种定位方法由于采用的是点接触,可在最大范围内消除误差。目前还有不少人不知道使用基准球定位的方法。使用基准球进行定位不但容易保证精度,且在工件形状复杂的情况下,能方便地实现分中;电极对基准球找中心的过程避免了电极作较大行程的移动,节省了操作时间;对于多个工件加工的情况,不需利用电极多次分中,只要对基准球分一次中即可,节省了大量的操作时间,多电极加工中优势尤为明显。另一个提高重复定位精度最好办法是采用快速装夹的定位系统,如3R和EROWA等装置,电极和工件都可快速换装,且可达到理想的定位效果,能极大地提高加工效率。
3.2冲液的方式与大小
电火花加工过程中,为了将加工过程中产生的气体、电蚀物等及时排除,必然高效率地排出加工屑,为此,应使用合理的冲液方式,控制好冲液压力,使加工稳定进行,提高加工效率。一般都要冲油或抽油。适当增加冲油压力会使加工速度提高,但冲油压力超过某一数值后,再继续增加,加工速度则略有降低。
4其他
4.1机床的加工性能
机床的性能好是实现高效率放电加工的前提条件。脉冲电源对提升加工速度起着极其重要的作用,脉冲电源性能的好坏决定着放电加工微观过程的优劣,决定着精加工中小放电间隙条件下能否稳定、高效地完成加工。自适应电源在加工中的自适应调节,对达到较高的加工效率有极其重要的作用。专家系统等智能技术使机床操作更容易,缩短了编程、操作的时间,配备ATC装置的全自动机床操作过程不需人工干预,可连续地自动运行加工,大大提高了加工效率。机床的抬刀技术上对加工速度也有一定的影响,如主轴采用很高加速度进给加工对提高深窄小缝的加工效率具有明显的作用。
4.2工作液的影响
选用不同的工作液,加工速度也不相同。目前电火花加工使用合成型电火花工作液。不同电火花加工工作液各自的特点有所差异,应综合考虑进行选择。镜面加工的时间一般都较长,使用混粉工作液(在工作液中加入一定比例的导电的粉末,如硅粉、铬粉、镁粉等)可大幅度提高加工效率。
4.3工件材料的影响
在同样的加工条件下,选用不同的工件材料,加工速度也不同。这主要取决于工件材料的物理性能(熔点、沸点、热导率、比热容、熔化热、汽化热等)。如电火花加工铝的效率非常高,但加工硬质合金的效率相当低。
5结束语
在实际加工中,影响电火花加工效率的因素众多。应根据加工对象的具体要求,进行综合考虑,把握好工艺的各个环节,才能使电火花加工机床达到高的加工效率。
苏州率尔捷机电科技有限公司目前开发生产的电加工机床产品主要有:数控电火花精密微孔加工机床,数控及普通电火花高速小孔加工机床,电化学去毛刺机床,数控电火花线切割机床,数控及普通电火花成形加工机床,电火花取断丝锥机,离心盘数控电火花穿孔机床。公司拥有自主开发电火花数控系统。公司可根据客户特殊要求,量身定制各种电火花加工专机,同时可为客户提供整套电加工解决方案,为客户在尖端制造领域提供技术支持和帮助。企业网址 http://www.szsej.com http://www.sej-edm.com
数控电火花机床加工效率直接相关的三大方面:电火花加工工艺、数控电火花加工机床的调整、电火花加工操作。根据这三方面详细探讨了提高电火花加工效率的工艺措施,希望可帮助企业解决一些实际问题。
1数控电火花加工工艺相关的要点
1.1要用机械加工去除大部分材料
工件的加工部位在进行电火花加工之前,要先用机械加工方法进行粗加工,仅将刀具精铣困难或无法精铣的部位留给电火花加工,这样能使电火花加工的材料量大为减少,可大幅度提高电火花加工效率。
如怕工作的麻烦,不进行机械粗加工就直接进行电火花加工,会导致电火花加工的效率极其低下,这就需正确认识电火花加工这种工艺方法的加工速度。电火花加工是靠微观的热融化过程一点点蚀除材料的,比起机械切削加工去除材料的过程要慢得多。对于大的型腔,即使是进行了机械粗加工,如给电火花加工留的余量过多也会降低加工效率。
2根据加工情况决定工艺方法
电火花加工有单电极直接成形工艺、多电极更换成形工艺等。选择工艺时不仅要考虑加工速度,还应详细考虑加工精度和表面粗糙度要求。单电极直接成形工艺只用一只电极加工出所需的型腔形状,这种工艺方法用于加工形状简单、精度要求不高的型腔,不需进行重复的装夹操作,可提高电火花加工的效率。对于加工要求较高的场合,通常采用多电极加工的工艺方法。首先用粗加工电极蚀除大量材料,然后用精加工电极进行精加工,精加工时还可考虑换用多个电极来补偿电极的损耗。
如在精度要求较高的加工场合,只使用一只电极来进行加工,这种因对工艺认识不够,本想通过减少电极数目来提高加工效率,而实际在加工过程却因为不能选用较大的电参数进行粗加工,导致加工的效率极其低下;另一种情况是,在加工要求不高的情况下,使用多个电极来进行加工,也必然会降低加工效率。
1.3合理选用电极材料
电极材料的选取直接关系到放电的效果,在很大程度上,材料的选取是否恰当,决定了放电速度、加工精度及表面粗糙度的最终情况。应根据不同类型模具加工的实际需求,有针对性地进行电极材料的选用。电火花加工通常使用紫铜电极和石墨电极。很多模具企业在选择电极材料时,很少进行考虑,大小电极一律习惯选用同种电极材料,这种做法会影响电火花加工的效率。
紫铜做电极较容易获得稳定的加工状态,可获得轮廓清晰的型腔,加工表面粗糙度值低,通常适用于低损耗的加工条件,由于低损耗加工的平均电流较小,且不适合大电流加工,其生产率并不高;石墨电极在加工蚀除量较大的情况下能实现低损耗、高速粗加工,但在精加工中放电稳定性较差,容易过渡到电弧放电,因而能选取损耗较大的加工参数来加工。
大多企业使用紫铜作为电极材料。而根据加工经验,使用石墨电极加工锻模的大型腔,其加工速度高,比使用紫铜电极可节省约1/3的时间;也有些企业认识到石墨电极的优越性,不分场合习惯选用石墨电极,导致模具在表面粗糙度要求低于的加工场合,始终难以稳定地达到加工要求,于是反复进行返修加工,极大地降低了加工效率,如选用紫铜电极,问题将会迎刃而解。可见选择电极材料时,应根据加工要求作出合理的选择。
1.4确定适当的电极缩放量
电极缩放量的选取要考虑多方面的因素。电火花加工有平动和不平动两种加工方式,数控电火花加工机床一般都可进行平动加工,而传统电火花加工机床如没有安装平动头就不能进行平动加工。这两种加工方式的电极缩放量选取是有区别的。
在不采用平动加工时,加工尺寸主要取决于精加工的控制。确定精加工电极缩放量时应先考虑好为达到预定表面粗糙度要选用的电参数条件,明确该条件下火花间隙的大小,再确定电极缩放量,一般取单侧0.02~0.06mm;确定粗加工电极缩放量时以考虑加工速度和为精加工预留适当余量为标准,一般取单侧0.15~0.25mm。
在采用电极平动加工时,加工的尺寸精度取决于对放电间隙、电极缩放量和平动量的控制。由于平动量的大小是可控的,所以可根据放电间隙的大小调节平动量,这样较容易控制加工的尺寸,电极缩放量的大小也就可相对大一些,尤其是在精加工时;总之可根据具体情况来灵活选取。粗加工中一般不用平动加工,电极缩放量取单侧0.15~0.30mm。精加工采用多段加工条件用平动的方法来改善排屑状况,达到稳定的加工,可获得侧面与底面更均匀的表面粗糙度。电极的缩放量常取0.05~0.15mm。
模具的电火花加工中,通常会因电极缩放量取得太小不能选用较大的放电条件而导致加工效率低下。如在加工允许的情况下,粗加工电极的缩放量取单侧0.30mm选用的电参数比取单侧0.15mm的电参数要提高速度在2~3倍以上。平动加工时精加工电极可根据加工情况,适当增大电极缩放量有利于提高加工速度。必须注意,增大电极缩放量后必须相应提高放电参数的能量,且不可盲目增大电极缩放量,否则反而会降低加工效率。如粗加工将电极缩放量取单侧0.80mm,而实际加工虽选择了较大的放电参数,但实际的放电间隙可能只有单侧0.30mm左右,那么将会为后续加工留下了较多的材料余量,必将降低加工效率。数控电火花加工机床如按传统机床的电极缩放方法,不利用平动加工的功能,必将降低加工效率,尤其是在精加工中。如电极缩放量取单侧0.03mm,那么只能选用一个较小的放电参数进行加工,如粗加工中的材料余量稍多的话,甚至可能产生无法加工的情况;如将电极缩放量增加到单侧0.08mm,那么加工的放电参数可增大,可很快地将材料余量去除,然后再利用平动功能来逐步修光侧面。对于加工电极是圆形、方形的更应如此。普通加工中适当增大电极缩放量并不会对形状造成多大影响,精密加工时才应特殊对待。
1.5电极设计考虑"面积效应"
"面积效应"是指电火花加工中因加工面积变化引起加工速度等工艺指标变化的效应。当电火花加工的面积小到某一临界值时,加工速度会显著降低。因为加工面积小,在单位面积上脉冲放电过分集中,致使放电间隙的电蚀产物排除不畅,同时,会产生气体排除液体的现象,造成放电加工在气体介质中进行,而大大降低加工速度。因此设计电极时要考虑不要拆分加工面积太小的电极,多使用整体式电极。但也要注意,当整体式电极面积较大,且加工深度较深、排屑困难的情况下,应考虑将整体电极分拆成几个电极进行分次加工,可根据型腔的几何形状把电极分解成主型腔电极和副型腔电极。否则在加工中会出现放电不稳定的情况,导致加工效率低下、精度难以保证等不良情况。
2数控电火花加工机床调整的要点
2.1电参数的调节
电参数选择的好坏,直接影响加工的各项工艺指标。电参数调节的最终目的是为了达到预定的加工尺寸、表面粗糙度要求,达到较高的加工效率。电参数调节时应考虑:电极数目、电极损耗、加工表面粗糙度要求、电极缩放量、加工面积、加工深度等基本因素。
目前数控电火花加工机床的智能性已有了很大的提高,机床储存有针对各种材料组合加工的大量成套参数,只需在编程过程中按编程要求输入工艺条件,即可自动选择、配置电参数。加工中机床依靠智能化控制技术(如"模糊控制"技术),由计算机监测、判断加工间隙的状态,自动微调电参数,保持稳定的放电加工,达到较高的加工效率。先进的智能化电火花加工机床的电参数数据库能满足一般加工要求,且极大地降低了机床对操作人员的技能要求。而传统电火花加工机床要求操作者具有丰富的工作经验,能根据加工要求灵活配置电参数。
机床的智能控制技术并不是万能的,故不能忽视人工调整电参数的作用。尤其像在深孔加工、大锥度加工、大面积加工等一些较特殊的加工场合,人工调整电参数就显得很有必要。调整电参数时,应优先考虑调整电参数主规准以外的参数,如抬刀高度、放电时间、抬刀速度等;其次可按次序考虑调整脉冲间隔、脉冲宽度、加工电流等,特殊材料加工可试用负极性加工(电极为负极)。在加工状态稳定的前提下,减少抬刀动作及幅度、降低脉冲间隔、增大加工电流有利于提高加工效率。但在加工不稳定的情况下,一定要保持勤抬刀,适当选用较大的脉冲间隔,否则反而会降低加工效率,甚至引起电弧放电,使加工过程不能正常进行。根据加工经验,适当保守地进行电参数的调节,可维持加工的正常进行,且可获得较高的加工效率。
脉冲宽度对加工速度有较大的影响,但一些技术人员在认识脉冲宽度对加工速度的影响上存在误区。有的认为将脉冲宽度增大可提高加工速度,有的则认为将脉冲宽度降低可提高加工速度。理论上:脉冲峰值电流一定时,脉冲宽度增加,加工速度随之增加,脉冲宽度增加到一定数值时,加工速度最高,此后再继续增加脉冲宽度,加工速度反而下降。但在实际生产中,对脉冲宽度必须要有一个量的认识。根据大量的加工实例,这里必须指出:最高加工速度对应的脉冲宽度往往很小,因此电极损耗较大,在很多情况下不宜采用,而实际加工中机床选配的电规准一般都考虑到降低电极损耗。那么,在低损耗加工规准中,如加大脉冲宽度,加工速度必然降低,降低脉冲宽度,加工速度会得到一定程度的提升。
2.2加工留量的控制
数控电火花加工是用多个条件段来进行加工的,条件段之间要有一定的加工留量。如加工要求的深度为5mm,电极缩放量为单侧0.15mm。设使用的电规准从大到小分3段来进行加工,则根据各档电规准放电间隙的大小来设置进给深度和平动半径:第一个规准进给深度为4.85mm,平动半径为0.02mm,第二个规准进给深度为4.92mm,平动半径为0.13mm,第三个规准进给深度为4.97mm,平动半径为0.17mm。各条件段之间加工留量大小的控制与加工效率有很大的关系。适当减少加工留量能提高电火花加工效率,尤其是在大面积的精加工场合作用显著。如将上例中第一个规准进给深度改为4.90mm,平动半径为0.10mm,第二个规准进给深度为4.95mm,平动半径为0.15mm,第三个规准不变,则可在一定程度上提高加工效率。
数控电火花加工机床自动编程时给出的加工留量,是以保证表面粗糙度为前提的,相对来说较保守,为了进一步提高加工效率,可根据加工要求修改自动编程生成程序的加工留量。但必须注意,减少加工留量必须要保证下一个加工规准能修光上一个加工规准。另外,减少加工留量对小面积加工的效率提高意义并不大。
2.3平动加工的选择
平动加工是数控电火花加工的一种重要工艺方法。不同的数控电火花加工机床其平动加工的方式有所区别,应根据所用机床灵活、合理应用平动加工。某数控电火花加工机床的平动加工方式有两种:自由平动和伺服平动。自由平动是指主轴伺服加工时,另外两轴同时按一定轨迹作扩大运动,一直加工到指定深度。伺服平动是指主轴加工到指定深度后另外两轴按一定的轨迹作扩大运动。自由平动一般用于浅表加工,加工时边打边平动可改善排屑性能,提高加工速度,减少积碳;但对于深度较深的场合,却会降低加工速度,增大电极的边角损耗。伺服平动一般用于加工深度较深的加工场合,先加工完底面再修侧面,深度较浅时其加工效果不如自由平动,它也常用在加工型腔侧壁的沟槽、环,还可用在其他两轴平动的场合等。
2.4定时加工
数控电火花加工机床一般都具有定时加工功能,可用于控制面积较大电极精加工的最后几段电参数的加工时间。精加工时电火花的电蚀能力非常弱,由于间隙内加工屑及其他因素的影响,需很长的加工时间。由于最后几个条件的尺寸变化已很小,实际上我们只要加工到要求的表面粗糙度后就可结束加工,可根据经验采用定时加工方法,这样可大幅度地提高精加工效率。
2.5改变垂直伺服加工的方法
目前大多数控电火化加工机床可实现横向加工、多轴联动加工。但这些功能在模具企业中并没有得到很好的应用。如能充分发挥机床的功能,可使机床的加工效率得到提高。如注塑模的成形镶件四周有较薄、较深的胶位,这些部位如采用Z轴伺服加工,会因局部放电面积小,加工深度大,加工过程中就会发生放电不稳定的现象,加工速度缓慢。若通过改善工艺方法,利用数控电火花加工机床的横向伺服功能,使电极作横向伺服加工,加工速度可比采用Z轴伺服加工提高数倍。模具"清角加工"因加工部位面积小而发生放电不稳定的现象,采用X、Y、Z3轴联动的方法,即斜向加工,可使放电加工稳定,提高加工效率。
3数控电火花加工操作的要点
3.1提高重复定位精度
模具电火花加工往往需使用很多个电极进行,这时需进行重复定位。实际加工中,重复定位精度也是影响加工效率的一个重要因素,这些情况主要发生在精加工中。如第一个电极在对深度时没有对准,导致第一次加工的深度浅了,那么第二次加工在必须保证加工深度的情况下,要加工的材料量必然增加,精加工中又不能选用大的电规准,这就导致了加工效率低下。根据加工经验,如像接近30cm2的大面积加工,在精加工规准下,多加工0.02mm的深度,将花费1h以上的加工时间;还有如第一个电极加工完成后,第二个电极加工的位置与第一个电极的加工位置存在较大差别,一个侧面修不到,另一个侧面的加工量增多,这种情况也会降低加工效率。
利用电极与工件进行接触感知的定位方法在模具企业被广泛采用。这种定位方法相对简单,是操作人员非常熟悉的。但这种定位方法的误差较大,难以保证稳定的定位精度,因定位超差导致的加工异常问题时有发生,降低了加工效率。为了提高重复定位精度,可采用间接定位方法。如利用基准球进行间接定位,这种定位方法由于采用的是点接触,可在最大范围内消除误差。目前还有不少人不知道使用基准球定位的方法。使用基准球进行定位不但容易保证精度,且在工件形状复杂的情况下,能方便地实现分中;电极对基准球找中心的过程避免了电极作较大行程的移动,节省了操作时间;对于多个工件加工的情况,不需利用电极多次分中,只要对基准球分一次中即可,节省了大量的操作时间,多电极加工中优势尤为明显。另一个提高重复定位精度最好办法是采用快速装夹的定位系统,如3R和EROWA等装置,电极和工件都可快速换装,且可达到理想的定位效果,能极大地提高加工效率。
3.2冲液的方式与大小
电火花加工过程中,为了将加工过程中产生的气体、电蚀物等及时排除,必然高效率地排出加工屑,为此,应使用合理的冲液方式,控制好冲液压力,使加工稳定进行,提高加工效率。一般都要冲油或抽油。适当增加冲油压力会使加工速度提高,但冲油压力超过某一数值后,再继续增加,加工速度则略有降低。
4其他
4.1机床的加工性能
机床的性能好是实现高效率放电加工的前提条件。脉冲电源对提升加工速度起着极其重要的作用,脉冲电源性能的好坏决定着放电加工微观过程的优劣,决定着精加工中小放电间隙条件下能否稳定、高效地完成加工。自适应电源在加工中的自适应调节,对达到较高的加工效率有极其重要的作用。专家系统等智能技术使机床操作更容易,缩短了编程、操作的时间,配备ATC装置的全自动机床操作过程不需人工干预,可连续地自动运行加工,大大提高了加工效率。机床的抬刀技术上对加工速度也有一定的影响,如主轴采用很高加速度进给加工对提高深窄小缝的加工效率具有明显的作用。
4.2工作液的影响
选用不同的工作液,加工速度也不相同。目前电火花加工使用合成型电火花工作液。不同电火花加工工作液各自的特点有所差异,应综合考虑进行选择。镜面加工的时间一般都较长,使用混粉工作液(在工作液中加入一定比例的导电的粉末,如硅粉、铬粉、镁粉等)可大幅度提高加工效率。
4.3工件材料的影响
在同样的加工条件下,选用不同的工件材料,加工速度也不同。这主要取决于工件材料的物理性能(熔点、沸点、热导率、比热容、熔化热、汽化热等)。如电火花加工铝的效率非常高,但加工硬质合金的效率相当低。
5结束语
在实际加工中,影响电火花加工效率的因素众多。应根据加工对象的具体要求,进行综合考虑,把握好工艺的各个环节,才能使电火花加工机床达到高的加工效率。
苏州率尔捷机电科技有限公司目前开发生产的电加工机床产品主要有:数控电火花精密微孔加工机床,数控及普通电火花高速小孔加工机床,电化学去毛刺机床,数控电火花线切割机床,数控及普通电火花成形加工机床,电火花取断丝锥机,离心盘数控电火花穿孔机床。公司拥有自主开发电火花数控系统。公司可根据客户特殊要求,量身定制各种电火花加工专机,同时可为客户提供整套电加工解决方案,为客户在尖端制造领域提供技术支持和帮助。企业网址 http://www.szsej.com http://www.sej-edm.com